Plastic Machining or Injection Molding Debate
Why pay for expensive tooling when you can have a part like this at a fraction of the cost? We’ve been getting a lot of questions on the subject of Plastic Machining vs. Molding.
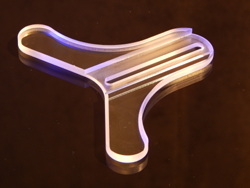
If you are at the cross road of determining whether your required plastic component should be produced by machining or injection molding, here are some facts to consider. The most obvious question is “what is the plastic”? There are many plastics that cannot be molded, or can cause issues depending on expectations for the finished part, especially if a smooth uniform surface is required. The process of transferring plastic into a mold leaves behind surface imperfections on the finished product. During the injection molding process, plastic flows through runners and is introduced into a cavity through a gate. The gate meters the flow of plastic as it fills the part. The consequence of the gate is that when the finished parts are removed from the mold, the gates leave a slight cosmetic imperfection. In addition, many molds use knockout pins to push the part out of the cavity after cooling. These pins leave a slight depression in the place where they contact the part.
Here is What Machining Plastic Can Provide
Machining plastic materials offer minimal tooling and no expensive molds are required.
When the need for part re-designs and revisions are necessary, the transition becomes easy, seamless, fast and cost effective. Machining plastic parts can provide certain materials with closer and tighter tolerances.
When machining plastic components you get unlimited material options, many of which would be impossible to mold. Threads and undercuts with multiple angles can be incorporated into the part with ease.
*Always keep this in mind once you create a mold, you cannot easily change it. Revisions, updates even slight changes will be costly.
Plastics Machining vs. Plastics Molding
Not sure if you should machine or mold? Some interesting points to consider before you make that costly decision
Plastic or Metal?
Before you lock in with metal in your next application, consider plastic or thermoset materials. Some interesting facts for you to consider
Heat Forming Plastics
A look at our plastic heat form process and value added options for secondary manufacturing assemblies and hardware installation.