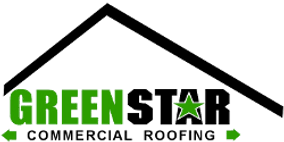
Repair and replace flat and metal roof systems.
GREEN STAR COMMERCIAL ROOFING
3031 LBJ FWY Sye. 1295
Dallas, TX 75244
Tel: 469.656.5264 888.556.9265
Online Resource Directory of U.S. Manufacturers
Repair and replace flat and metal roof systems.
3031 LBJ FWY Sye. 1295
Dallas, TX 75244
Tel: 469.656.5264 888.556.9265
Local 24-hour mobile locksmith service provider for Pittsburgh Pennsylvania.
1514 Rockland Avenue
Mobile, PA 15216
Tel: 412.780.6423
We have the right people and the right technology to make sure your freight is delivered on time, every time.
141 S. Meridian St.
Indianapolis, IN 46885
46885
Tel: 866.971.7768
Fluid Slip is a term commonly used to describe the migration of liquid around the internal moving parts of gear, lobe, and vane pumps. It is the volumetric difference between physical component displacement and liquid throughput of a pump system. Slip loss refers to the liquid that passes through the clearance space (approximately 0.00005 inches) between the piston and the cylinder wall. Since this clearance represents a restrictive passage of essentially constant dimension, the slip rate is determined by viscosity, pressure and time.
Assuming constant liquid viscosity and pressure, slip will be a smaller factor in a high repetition rate pump (short time per stroke) than in a low repetition rate pump. As viscosity increases and pressure decreases, time becomes a less significant contributor to slip loss. The clearance can be modified to compensate for viscosity. The clearance between the piston and cylinder wall must be optimized for the liquid being pumped in order to minimize the loss due to fluid slip.
In order to minimize fluid slip, the reservoir height and tip height need to be considered. As a general rule, the reservoir height and tip height should be equal. A fluid’s viscosity will play a part in this determination. One way to determine the optimal position of the reservoir and tip is to prime the input and output lines with fluid and observe the output line for fluid movement during idle time. If the fluid moves back in the line, raise the reservoir. If the fluid drips from the tubing, lower the reservoir. The goal is to achieve zero pressure differential over the pump.
Fluid Slip is an important factor to consider through the design and build stages of any pump or pump component. If you have any questions about fluid slip, please contact us and we would be happy to help.
EYPM is an engineering, integration and development company focused on providing solutions and support in the wide field of engineering, maintenance and services in the manufacturing industry
16010 Barkers Point Ln Suite 220
Houston, TX
77079
Tel: +1 (832) 392-5531
Why pay for expensive tooling when you can have a part like this at a fraction of the cost? We’ve been getting a lot of questions on the subject of Plastic Machining vs. Molding.
If you are at the cross road of determining whether your required plastic component should be produced by machining or injection molding, here are some facts to consider. The most obvious question is “what is the plastic”? There are many plastics that cannot be molded, or can cause issues depending on expectations for the finished part, especially if a smooth uniform surface is required. The process of transferring plastic into a mold leaves behind surface imperfections on the finished product. During the injection molding process, plastic flows through runners and is introduced into a cavity through a gate. The gate meters the flow of plastic as it fills the part. The consequence of the gate is that when the finished parts are removed from the mold, the gates leave a slight cosmetic imperfection. In addition, many molds use knockout pins to push the part out of the cavity after cooling. These pins leave a slight depression in the place where they contact the part.
Here is What Machining Plastic Can Provide
Machining plastic materials offer minimal tooling and no expensive molds are required.
When the need for part re-designs and revisions are necessary, the transition becomes easy, seamless, fast and cost effective. Machining plastic parts can provide certain materials with closer and tighter tolerances.
When machining plastic components you get unlimited material options, many of which would be impossible to mold. Threads and undercuts with multiple angles can be incorporated into the part with ease.
*Always keep this in mind once you create a mold, you cannot easily change it. Revisions, updates even slight changes will be costly.
Plastics Machining vs. Plastics Molding
Not sure if you should machine or mold? Some interesting points to consider before you make that costly decision
Plastic or Metal?
Before you lock in with metal in your next application, consider plastic or thermoset materials. Some interesting facts for you to consider
Heat Forming Plastics
A look at our plastic heat form process and value added options for secondary manufacturing assemblies and hardware installation.
Whether you need a decon in response to a contamination or preventative decontamination of new or existing facilities, the ClorDiSys chlorine dioxide gas methodology provides complete decontamination of your facility all at once, with minimal equipment and minimal downtime. This gaseous system has the ability to achieve complete distribution and penetration to all surfaces within your facility, including cracks and crevices, which other methods can’t achieve.
American Instrument Exchange buys and sells used laboratory and scientific equipment. Our surplus lab equipment is reconditioned for many types of laboratories, including biotech, biomedical, medical research, chemical, pharmaceutical, and university and hospital research laboratories.
We have been a reliable source for used laboratory and scientific equipment since 1969. All lab equipment listed on our website is in stock and ships from our 30,000 square foot warehouse in Haverhill, MA. Our facilities include a fully equipped shop with highly trained technicians who thoroughly test each instrument before it reaches your laboratory.
Our new branding comes with a new company name and logo but TEMCO™ has produced high quality precision machined parts for over half a century. As an ISO 9001 AS9100 certified manufacturer catering to the world's most demanding industries, TEMCO™ has solutions for your manufacturing needs.
We are proud to be a top choice for manufacturing and machining precision parts for companies in many industries and markets. Our work with contractors in the aerospace and defense sector has won us awards.
As an ISO 9001:2015 and AS9100D registered and certified manufacturer, TEMCO™ continues to house its operations in a 50,000 square foot, climate-controlled facility. Quality, on-time delivery, and safety are the pillars to our objective to provide 100% customer satisfaction.
With the capacity to offer quick-to-market services, short run production, high volume manufacturing, LTA's and Kanban ordering system, we pride ourselves as being a true full-service precision manufacturer.
The shop features high speed machining centers, Electrical Discharge Machining (EDM), Assembly and the latest Computer Numerically Controlled Machines (CMMs) to support precision machining of complex shapes or difficult materials.
Polyonics®, a leader in high-temperature and harsh environment label and tag materials, announces that industry veteran Alvin Poon has joined as Director of Sales and Business Development in the Asia Pacific region. The announcement comes as part of Polyonics’ forward-looking commitment on creating strong loyalty among its business partners and customers using the company’s unique personal chemistry approach and innovative engineered solutions, including those for electronics manufacturers in the Asian market.
“I am very excited to have Alvin join our team here at Polyonics. We pride ourselves on not only having the highest quality products but also on having the best team of people working together to solve our customers’ most challenging label applications. Alvin’s experience, integrity and professionalism will strengthen our presence in the Asia Pacific region and enable us to grow through relationships with our partners and customers in all of our served markets,” said Jim Clemente, President and CEO of Polyonics.
Poon’s career in the labels industry started back in the mid-nineties, including sales roles at Brady Corporation and Honeywell (former LXE). In 2011, he was the Labels & Packaging Category Manager for HP’s Indigo Division in Asia Pacific and Japan. Most recently, Poon was the Regional Business Development Manager for Epson, where he drove collaboration company-wide to ensure successful project delivery for product launches and spearheaded the adoption of an agile channel structure to execute efficient and more effective routes to market.
Poon will draw from his over 24 years of experience in the label industry to strengthen relationships with hundreds of industry partners and customers across the region. “I'm very excited and honored to join Polyonics. Polyonics is renowned for its strong customer focus and outstanding quality. I believe we will continue to bring innovative solutions and products that performs in high temperature environments to the industries we serve,” said Poon.
According to Clemente, the company’s then insightful decision to follow and support electronics manufacturers as they moved to Asia in the late 1990s was a key factor in Polyonics’ success over the past 25 years. “The Asia-Pacific market is clearly very important to the success of our core business and under Alvin’s leadership, I’m confident the team will continue to drive success in the region,” concluded Clemente.
For more information about Polyonics topcoats and label materials, please visit www.polyonics.com.
A major application for liquid dispensing systems is drug addiction management. Clinics and centers detoxifying patients from opioid addictions often utilize methadone. As reported in 2011 by the National Survey of Substance Abuse Treatment Services, over 306,000 people in the United States receive methadone for substance abuse each year. This medication helps to minimize narcotic withdrawal symptoms and decrease cravings, all without producing the same euphoric effects as drugs like heroine or prescription painkillers.
Administering methadone requires a strict protocol where exact dosages are consistently taken at a scheduled time. When this protocol isn’t followed, there is a risk of overdose. In fact, there are about 5,000 methadone overdose deaths each year, according to Time Magazine (2012).
IVEK has a complete line of methadone dispensers to meet the diverse needs of our customers. All our systems are durable, accurate, and user-friendly. Our most popular system, the Digispense DS1000, is capable of extremely high precision and repeatability. This system features positive displacement ceramic pumps and a whisper-quiet, high-speed brushless DC motor. With only one moving part in the fluid path, systems operate for many years without measurable wear. Also included are factory-made tubing kits with bottle cap connections and a volumetric flask for accuracy checks. The DS1000 is easy to control from the USB or RS232 Interface, which is supported by most addiction treatment software.
For customers who need a more transportable option, we recently released an all-in-one Controlled Substance Dispensing Station (CSDS). This station is portable, secure and easy to clean. It features shorter tubing runs for faster priming and less waste, a fixed dispense tip for no mess dosing, lockable latches, and adjustable spill tray locations for varying cup sizes. We’re currently offering FREE installation and calibration of your existing pump with any CSDS purchase.
Last among our dispensers is the MethaSpense system, which was specifically designed for use in drug addiction management clinics. This system has a two-position bottle cradle that allows for refilling without the loss of prime to the pump or having to transfer liquid from one bottle to another. This design minimizes fluid loss and enhances record keeping while providing a more sanitary diversion of fluid. Our exclusive ‘Liquid Eye’ bubble detector is also integrated. This detector uses an alarm to alert the operator of any air in the fluid line that may compromise precision before a dose is dispensed.
The MethaSpense system is housed in a stainless-steel case that can be easily moved and secured during non-operating hours. The system accepts a variety of bottle sizes and comes with a
patented ‘Zero Transfer’ bottle holder. Key lock security ensures only those permitted are given access to the supply bottle. The system is also easily integrated with commercial patient management software.
IVEK has been manufacturing controlled substance dispensing systems for over 30 years, allowing us to refine our products with customer feedback. Our systems are used in drug management programs worldwide.